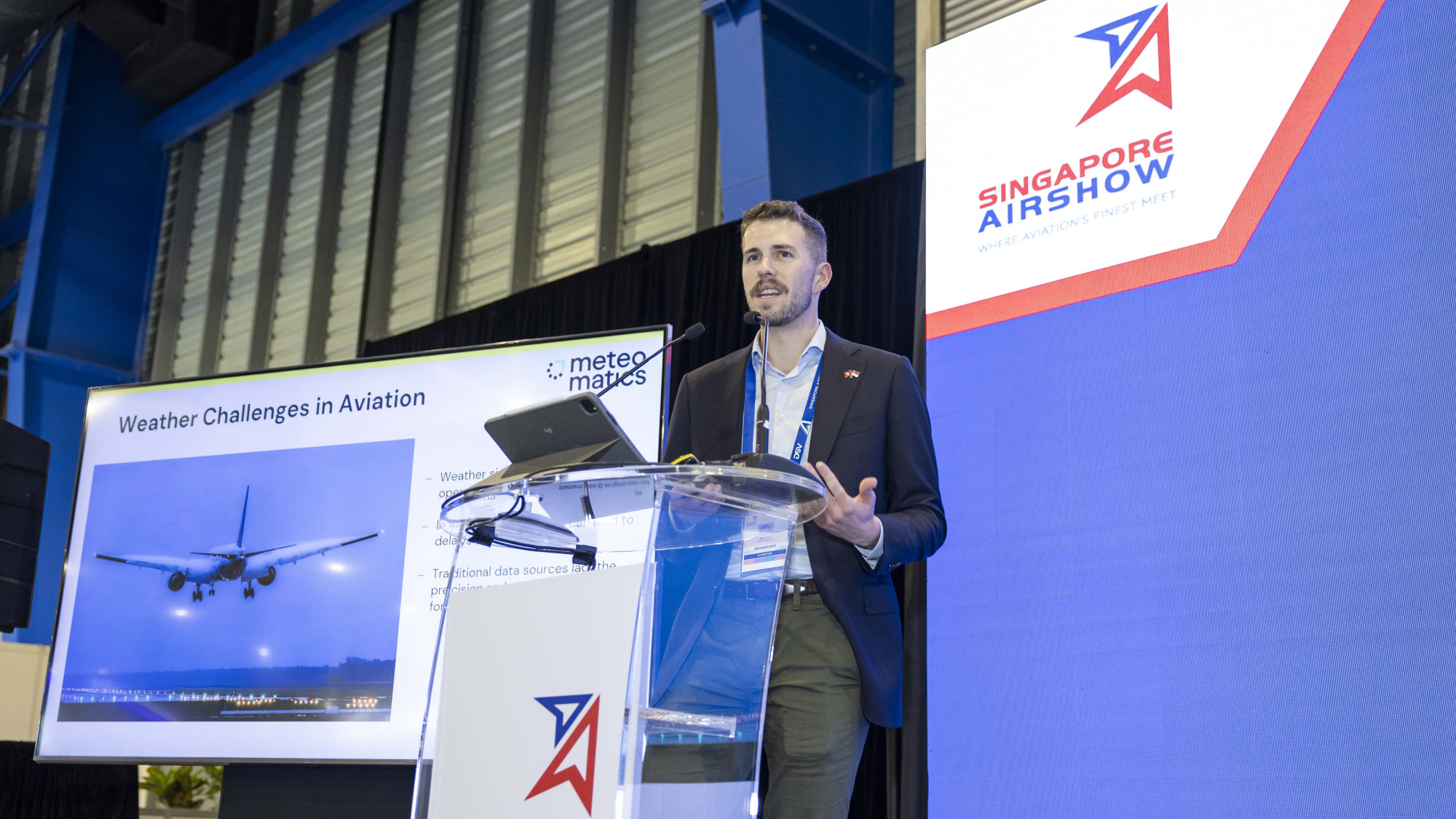
Programmes
Space Summit 2026
An Electrifying Race for Clean Energy Planes
An electrifying race for clean energy planes
As the aviation industry embraces sustainability, the race is on to develop commercially viable innovations that allow planes to fly on clean energy.
The ultimate goal is to eliminate reliance on conventional jet fuel to pave the way for flights resulting in low, or zero emissions.
Many companies are taking concrete steps to achieve these goals. As a result, various projects such as hydrogen powered planes, hybrid aircraft that use both electric batteries and synthetic fuels have become more prevalent in the recent years.
Exciting developments include the upcoming debut of a first all-electric consumer aircraft by Eviation, Alice, in 20241.
![]() |
---|
Photo credit: Eviation
Besides this, one of the most promising innovations is the development of lithium metal batteries that have twice the energy density2 as standard lithium-ion.
The technology was developed by Cuberg, a Silicon Valley start-up acquired by EV battery giant Northvolt3.
Experts believe Cuberg’s innovation could see lithium metal batteries powering small planes within the decade – if the batteries can be scaled up to reach commercial viability.
So how important is this development in the quest for clean energy use in air travel? Experts from Rolls-Royce and Textron Aviation shed some light.
Interviewees:
Sophie Chittim, Energy Storage System Technologist, Rolls-Royce
Rob Scholl, Senior Vice President, eAviation, Textron Aviation
Are electric planes taking off soon?
While electric cars have become more prominent on the roads in recent years, the application for the aerospace industry needs more work.
Q: How promising is the development of lithium metal batteries that have twice the energy density as standard lithium-ion?
Sophie Chittim: A doubling of the energy density for batteries would be a leap forward for all-electric aviation. Battery powered aircraft are viable with today’s technologies but the types of aircraft and ranges that can be achieved are limited. An increase such as this would enable larger and more capable all-electric aircraft.
Q: What are the key similarities and differences between developing an electric car battery and electric plane batteries that can be used at high altitude and under reduced pressure?
Sophie Chittim: Both aerospace and automotive require high performance cells, however in general aerospace tend to focus on gravimetric energy density (energy per unit weight) whereas automotive have greater limits on volume.
I would say the key distinction for aerospace is the varying requirement for certification - as with all aviation products, burden of proof for certification and safety differs significantly from automotive which steers the industry towards more sophisticated materials and designs at a pack level.
Rob Scholl: There are some differences between the technology required for automotive and aerospace applications. As these continue to improve, we need to focus on developing battery management systems and regulatory frameworks that will allow this to come to fruition in aerospace.
Despite these gaps, it remains key for industry players to come together to optimise efficiencies in both the batteries and electric motor system.
Q: How important is it for battery makers to work with electric-motor developers to optimise efficiencies in both areas?
Sophie Chittim: In a fast-moving industry such as all electric aircraft, a level of collaboration across pioneers in the space will enable products to be brought to market more quickly. As Rolls-Royce is a propulsion system provider, we will naturally require a partnership with cell suppliers to enable effective integration within the packs and overall system we design. In the case of electric motors, working with a battery manufacturer, we can balance the trades between efficiency and weight to achieve a better optimised overall system.
By 2035, Rolls-Royce is planning to integrate more than 5 million battery cells per annum into modular systems. These modules will deliver market-leading energy density levels.
Aerospace-certified ESS solutions from Rolls-Royce will also power electric and hybrid-electric propulsion systems for eVTOLs (electric vertical takeoff and landing) in the Urban Air Mobility (UAM) market and fixed-wing aircraft, with up to 19 seats, in the commuter market.
Rob Scholl: With the emerging technologies now coming into aerospace, it’s vital that the entire supply chain works together not only to address technology challenges, but the entire framework of technology, regulation and operations.
Power VS Weight
While there are advancements in cell technology, there continues to be a significant gap between the power provided by jet fuels versus the power provided by batteries currently.
Jet fuel has an energy density of about 12,000 Wh/kg whereas commercially available lithium-ion batteries have an energy density4 at the cell level of about 250 Wh/kg. Now, this lithium metal batterie breakthrough has twice the energy density of lithium-ion batteries. While lithium metal batteries themselves have been around since the early 1960s, this proves that it has real promise for commercial application.
One of the persistent challenges that lithium metal batteries have faced are the dendrites that form during charging. These needle-shaped formations can penetrate and short the cell, possibly causing fires, which means the batteries cannot be recharged and used safely. However, the happy news is that this technological breakthrough addresses this issue too5.
A breakthrough is just the first step; more development is needed for these lithium metal batteries, and such technology is not expected to be commercially available until 2028.
This means that with the current technology, lithium-ion batteries can only power short range aircraft, given that weight is a critical component to improving the capabilities of an electric aircraft.
In order for electric planes to travel longer distances, the performance of the batteries need to improve.
Q: Some believe the latest innovation could see lithium metal batteries powering small planes within the decade – if the batteries can be scaled up to reach commercial viability. What does this mean for the future of electric aircraft?
Sophie Chittim: Lithium metal technologies available by 2030 would be an exciting prospect – as the technology matures, industry will grow to understand more about the scale-up and manufacturing. This will enable companies such as Rolls-Royce to design packs around these cells to make powering future aircraft a possibility.
Q: One of the challenges in developing electric batteries for air travel is being able to produce cells that are versatile enough to discharge energy quickly during take off and landing, but also enduring enough to keep the plane in flight for the duration of the journey. How close are we to achieving this?
Sophie Chittim: In fact, cells today and future cell projections seem very capable of achieving a good energy/power balance, particularly well-matched to conventional aircraft.
The power difference is much greater in vertical take-off and landing aircraft which amplifies the problem. Cells today can be optimised to achieve the power rates required for this, but it demonstrates the need for propulsion system providers to engage with cell suppliers to ensure these requirements can be built into overall cell specifications.
Rob Scholl: With emerging technologies now coming into aerospace, it’s vital that the entire supply chain works together not only to address technology challenges, but the entire framework of technology, regulations and operations.
Q: How can we increase the distance that a plane powered by electric batteries can travel?
Sophie Chittim: Broadly, this improvement will come by achieving a higher performance within the same weight. At a battery pack level, as our understanding of aerospace pack design matures, we will be able to reduce the weight overhead associated with this. At cell level, energy density is key for this – which is where chemistry advancements such as lithium metal can revolutionise what can be achieved with all-electric aircraft.
Rob Scholl: I think it goes back to looking at the entire supply chain or infrastructure related to this. Weight is a critical component to improving capabilities of electric aircraft require advanced composites or manufacturing. Unique aerodynamic profiles mean a lot of the challenges comes down to weight of entire aircraft and systems.
There’s a desire in the marketplace in general for new technology such as advancements in electric aircraft, due in part to increased urbanisation worldwide. While it may be an accepted technology by customers, the marketplace dynamics may not allow large scale adoption soon. The challenges are both regulatory and economic. It needs to make sense in both these aspects.
For electric aircraft to take to the skies, all parties along the value chain need to be committed to advance - in technology, regulations and funding. In order to achieve this, close partnerships among industry players will be crucial in shaping the future of the industry.
1https://robbreport.com/motors/aviation/eviation-alice-maiden-flight-2021-1234625186/
2Energy density refers to the amount of energy stored in the batteries per unit volume
3https://cuberg.net/news/why-this-battery-breakthrough-could-make-evs-cheaper
4Energy density is the amount of energy stored per unit volume.
5https://www.cnbc.com/2021/06/30/why-lithium-metal-batteries-could-replace-lithium-ion-batteries-in-evs.html